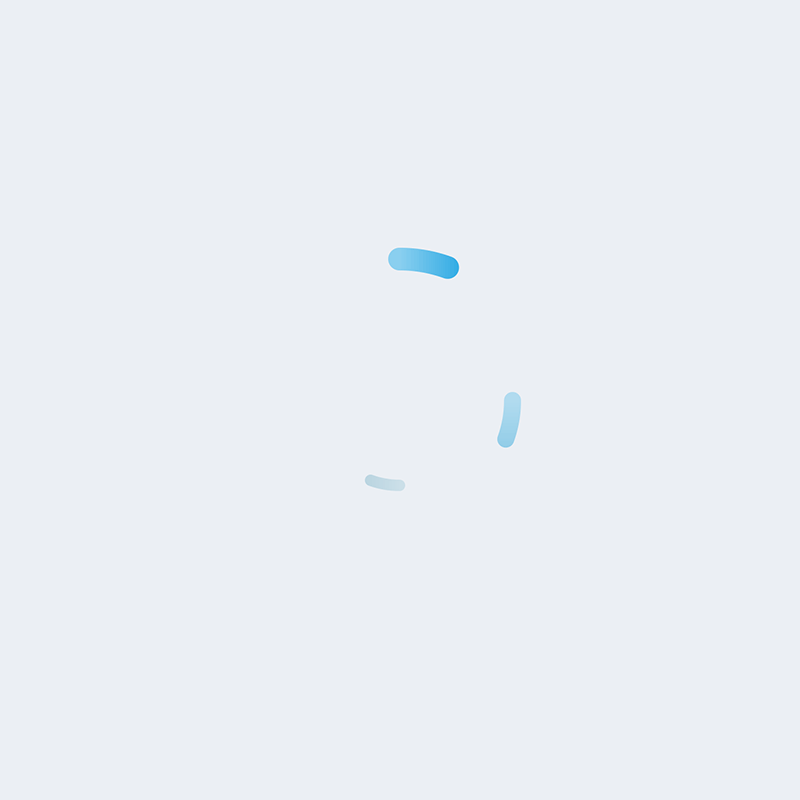
Shoes and Soles From the 3D Printer
Additive Manufacturing for a Perfectly Fitting Shape
Comfortable 3D Printing Solutions for Shoe Manufacturers and Their Customers
Personalization has been more than just a trend for a while now. As well as offering greater comfort to their wearers, custom shoe soles open up completely new possibilities for fashion customization. Additive manufacturing has the solution: Thanks to a fully digital process, trendy designs can be put together using scans of the sole of the foot, then transformed into custom-fitting shoe soles made from polymer materials by industrial 3D printing.
For contract manufacturers and shoemakers, the advantages are obvious. They can reliably deliver custom soles to their customers, allowing them to react quickly to new trends. At the same time, industrial 3D printing is extremely suitable for series production. It is characterized by high flexibility of material strength and structure, so that the products can be perfectly fitted to the wearer’s anatomy. The manufacturing process is also relatively cost-efficient.
3D printed shoe soles combine personal style with the demands of fashion. The manufacturing process guarantees maximum flexibility while also being cost-efficient.
Case Study Aetrex Worldwide, INC
Customized Insoles From the 3D Printer
Aetrex is a global leading manufacturer of foot scanning technology, orthoses and comfort shoes. In partnership with EOS, Aetrex uses a Digital Foam approach to make custom 3D printed soles. The production and delivery of the finished product is completed very quickly. The partnership between Aetrex and EOS resulted in a complete 3D printing value chain with digital production in a mainstream format.

Play video
The path to a customized mass product
Aetrex uses customer data collected using the Albert program, an innovative foot scanning system. The captured data is then sent to the EOS 3D printer. Based on the measurements of the individual pressure point distribution, the 3D printer then creates a 3D printed insole. The result is a product that is precisely tailored to the customer’s foot.
- “Mass customization” – adapting individual products to many different variants
- Sustainability – less material consumption, since any leftover material can be reused
- Improved ergonomics – the product fits better than conventionally manufactured soles
- Rapid availability – the sole is ready in less than 2 weeks
A Pair That Fits Together
Metal 3D printing is an exciting and disruptive technology. But initially I was skeptical whether its advantages would extend to meet our own requirements. Three years on, it has given us solutions for many projects that would not have been possible otherwise.
Dr. Jens Struckmeier | CTO | Founder of Cloud & Heat